The Critical Role of a Lab Ventilation Management Program Coordinator
Improperly designed and aging labs, especially with poor ventilation, can adversely affect safety, energy use, operating costs, and research results. Laboratory Ventilation Management Programs (LVMP) are one way to address this challenge and help maintain the safety and health of lab staff while contributing to broader energy reduction goals.
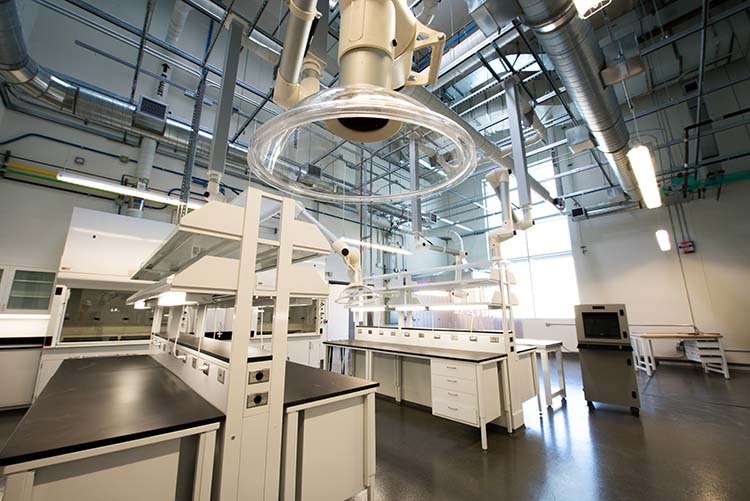
LVMPs are the primary way to control exposure to airborne hazards and improve air quality. The performance of a laboratory ventilation system depends on proper maintenance, room layout, and user behavior. As a component of a Smart Labs initiative, the LVMP utilizes a combination of physical, administrative, and management techniques to help optimize and maintain the performance of the exposure control devices (ECD) and laboratory ventilation systems.
When Los Alamos National Laboratory (LANL) developed their LVMP, they also introduced a crucial role, the LVMP coordinator. The coordinator serves as a liaison between various stakeholders and facilitates communication and coordination of tasks and activities necessary to monitor and manage laboratory facility operational activities, operation of the ventilation systems, and ECDs. Through this role, the LVMP coordinator helps spearhead initiatives while making sure the right representatives are brought to the table.
Additionally, the LVMP coordinator is responsible for finding ways to streamline processes across laboratory buildings and staff. The coordinator also provides training to facility managers, environmental safety and health, maintenance, and laboratory managers to promote safe, efficient, and dependable operation of the lab ventilation systems.
With more fume hoods running than ever before, LANL has been able to gain more traction and internal buy-in. Through LVMP, LANL was able to recently shut off two heating and ventilation units in one building, leading to savings of 12,000 kWh per month.
Coordinator Responsibilities
Task 1: Implementation and Administration of the Building LVMP
- Provide direction and coordinate LVMP activities between key stakeholders while continuously assessing on-going program performance and plan for changes in use or application.
- Help improve operational efficiencies and further safety measures in the laboratories.
- Provide training to key stakeholders and others associated with the execution of the LVMP.
Task 2: Document, Review, Organize, and Control
- Assist with reviewing existing design and construction documents related to the ventilation systems including engineering drawings, specifications, test and balance (TAB) and commissioning reports.
- Help control and monitor document updates.
- Consult on space planning and occupancy needs.
- Propose recommendations for the placement of processes within a laboratory environment.
Task 3: Monitoring HVAC Performance
- Monitor laboratory HVAC system operation and performance through review and analysis of building automation system screenshots and trend analysis.
- Report operational anomalies as they occur through approved organization channels (work orders and repairs) and assist with diagnostics and resolution.
- Monitor operation of the demand control ventilation system and track response events to update risk classifications.
- Assist facilities, maintenance, and contractors with troubleshooting system alarms and operational failures involving the lab ventilation systems.
- Conduct investigative tests to assist with problem diagnostics and assist with verifying proper operation of systems, lab environment, and laboratory hoods.
Task 4: Management of Change
- Assist LANL with implementation of a management of change process.
- Provide review and consultation on ventilation change requests.